Developing Corrosion Inhibitor Models
Presented at WaterTech '93, Houston Texas
Reprinted in Industrial Water Treatment Magazine
Robert J. Ferguson
French Creek Software
Kimberton & Hares Hill Road, Box 684
Kimberton, PA 19442 U.S.A.
Keywords: corrosion, indices, inhibitors, modeling
INTRODUCTION
Few tools are available for direct use by the cooling system chemist for the prediction of corrosion
rates in the presence and absence of corrosion inhibitors. The models which are available are used
primarily by research laboratories and the water treatment service companies as a service to their
customers. Models which predict the performance of a corrosion inhibitor versus inhibitor dosage
can be used to establish the economics for treatment to a given corrosion rate target. At a
minimum, such models could provide information on the relative treatment costs for achieving 1
mpy in a system, 2 mpy, 5 mpy or other targets.
The wide spread use of personal computers and the availability of PC based software have
provided the cooling water chemist with a method for in-depth water chemistry evaluation, and for
the application of statistical methods to modeling historical data bases of treatment results versus
water chemistry, operating parameters, and treatment levels.
Model development requires a baseline method for predicting the untreated corrosion rate as well
as models for predicting the corrosion rates in the presence of inhibitors.
SIMPLE INDICES AS INDICATORS OF CORROSIVITY
Calcium carbonate scale potential indices such as the theoretical Langelier Saturation Index have
been used as indicators of corrosivity of water towards mild steel under the assumption the if a
water is scale forming, corrosion rates will be negligible. As a corollary, waters that are not scale
forming are considered corrosive when interpreting the LSI. The Ryznar Stability index combines
empirical data with the theory of calcium carbonate saturation to predict the scale forming tendency
and mild steel corrosivity of a water. The same assumption applies to interpretation of the RSI.
Calcium carbonate is the sole parameter for determining the corrosivity of a water. Larson and
Skold used a data base of corrosion rate and type observations to formulate an index for the
corrosivity of water towards mild steel. (1) They found that alkalinity tended to reduce the corrosion
rates of mild steel and postulated that it is a natural inhibitor that participates in the formation of an
inhibitor film. Chloride and sulfate were found to increase the corrosivity of a water. This effect is
explained by the interference of these anions in the formation of a natural inhibitor film. Larson and
Skold proposed the use of the ratio of sulfate and chloride concentration to alkalinity as an
indicator of the corrosivity of a water towards mild steel. The simple indices provide indicators of
corrosivity of a water toward mid steel and have the further advantage of ease of calculation. The
are limited in their effectiveness. All of the indices have been used as independent variables in the
development of corrosion rate and inhibitor dosage models. TABLE_1 summarizes simple parameters
considered critical to corrosion modeling.
ADVANCED MODELS FOR CORROSION RATE
Pisigan and Singley developed several models for mild steel corrosion rate prediction from a
combination of static and dynamic laboratory test data.(2) They found that corrosion rates observed
in their tests could be correlated to chloride and sulfate, calcium, alkalinity, buffer capacity,
dissolved oxygen levels, and exposure. A high correlation (r2 = 0.90 to 0.98) was found between
corrosion rate and four to eight variable models. Davis used similar variables to develop a model
for corrosion rates in the presence of a specific inhibitor.(3) Other models have been developed for
internal use by major water treatment companies.
UNCERTAINTY IN MODELS
A common problem to all models is relating their predictions to real world corrosion in operating
cooling systems. Test data, by necessity, relies upon corrosion coupons or electrochemical
methods as the basis for measuring corrosion rates. On the plus side, these are the same techniques
used to monitor corrosion rates and treatment effectiveness in most cooling systems. Results can
very dramatically, even under the same water chemistry conditions. A recent paper outlines the
problem.(4) Corrosion rates on polished metal specimens were compared to those observed under
the same conditions using precorroded metal specimens. Measured rates where one to two orders
of magnitude higher on the precorroded coupons. They found the use of precorroded metal
specimens to be critical to the success of using laboratory data to model an operating system in the
field.
MODELS IN THIS PAPER
This paper uses the basic method outlined by Pisigan to develop a baseline correlation for
corrosion rate prediction, and for modeling the impact of inhibitors on corrosion rate. Models are
then used to predict the inhibitor level requirement to achieve a specified corrosion rate target.
Equation 1 is typical of the models used by Pisigan to correlate corrosion rates observed in
laboratory testing to water chemistry. Pisigan used models of_four (4) to eight (8) variables to
derive correlations for corrosion rate as a function of water chemistry. Equation 2 uses ion
association model concentrations for selected variables to develop correlations to similar variables.
Inhibitor concentration is included in the model to add the impact of inhibitors on corrosion rate.
_______________________(Cl)a1(SO4)a2 (Alk)a3 (DO)a4
EQUATION 1 ____Rate = __________________________
_______________________(Ca)a5 (B)a6 (Time)a7 (10LSI)a8
where:
- Cl is the chloride concentration,
- SO4 the sulfate concentration,
- Alk the total alkalinity,
- DO the dissolved oxygen level,
- Ca the calcium concentration,
- B the buffer capacity,
- Time the number of days of exposure,
- LSI, the Langelier Saturation Index, and
- a1 - a8 are regression coefficients.
__________________________(Cl)a1 (SO4)a2
EQUATION 2 Rate = K ________________________
_____________________(Ca)a3 (CO3)a4 (Inhib)a5
where
- K is a temperature dependent constant
- CO3 is the carbonate concentration, and
- Inhib is the corrosion inhibitor level.
Equation 2 is used to develop correlations through regression analysis. This paper illustrates the use
of such equations for two types of models: models derived from laboratory data, and models
derived from the experience of water treatment chemists. A baseline corrosion rate model is
developed from laboratory data, and a simple corrosion inhibitor model is developed for
orthophosphate.
THE BASELINE DATA
Two sets of data were used to develop a baseline model for predicting corrosion rates in the
absence of an inhibitor. The data published by Pisigan were modeled due to the use of correlations
derived from it as a Recommended Method.(5) A set of fifty six test runs analysis from unpublished
data were used for the working models due to their development in a dynamic test environment. (6)
The Pisigan data reflects static test conditions, while that supplied by Zisson resulted from dynamic
laboratory testing. Carbonate and bicarbonate concentrations used in the correlations were
calculated by the computer program used to develop the models. Analytical values for other ions
were used for the models. The software uses an ion association model to predict the most likely
concentrations of species in the water based upon equilibrium calculations. Estimates of species
concentrations (e.g. {CO3=}) and indices tend to be transportable between waters of widely
different composition when calculated using an ion association model. The ion association method
was used to provide the best probability for the development of broadly applicable models rather
than models limited to specific water qualities. Figure 1 depicts the predicted versus observed
values for the dynamic model. A strong correlation was observed for the prediction of mild steel
corrosion rates of 20 mpy or less. The model tends to over-predict in more corrosive waters. Table 2 outlines the water chemistry range covered by the baseline data. The baseline models
provide an untreated point of reference.
CORROSION INHIBITOR MODELS
Laboratory versus Experiential Model
A criticism of laboratory based models is that they do not necessarily represent the dynamic
conditions of operating field systems. Although laboratory based models have been used
successfully to select treatment programs and estimate the optimum treatment level, most people
prefer field experience or a combination of field and laboratory support for decisions. Many water
treatment personnel rely upon their experience to select treatments and initial treatment levels. If a
treatment provided the performance desired in a similar water, it is usually a good choice.
Experiential models are developed from field data of water chemistry, inhibitor dosages, and
treatment results. A model for orthophosphate dosage was developed based upon the experience
of fourteen water treatment personnel with an average of over ten years experience in treating a
broad range of cooling water. They were asked to recommend dosages for orthophosphate which
would provide corrosion results of 5 mils per year or less, general etch attack, for various waters.
Personnel included had worked with the major water treatment service companies. The water
chemistry included inthe survey ranged from low pH and low hardness to alkaline treatment
programs. Figure 2 profiles the predicted versus observed values for the model. The parameter
ranges for the observations are outlined in Table 2.
APPLICATION OF THE MODELS
The models were applied to a refinery cooling system to illustrate their practical use. The pH of the
system is controlled with sulfuric acid to minimize the scale potential for calcium carbonate and
calcium phosphate.Table 3 outlines the makeup and recirculating cooling water for the system.
High mild steel corrosion rates are expected in the system if left untreated (Figure 3).
The models are used by a computer program to model the cycled water chemistry and recommend
treatments using the following scheme:
First the makeup water is cycled to the target concentration ratio using computer simulation. The
pH is predicted based upon a pH - alkalinity relationship derived empirically for the specific
system. If pH control is in effect, acid feed requirements are calculated by the program, and the
alkalinity levels decreased and sulfate levels increased accordingly. Ion association model indices
are calculated on the pH adjusted water.
The second step is to calculate the recommended orthophosphate treatment level for the water
using the experiential model. The orthophosphate requirement is added to the recirculating water
chemistry by the computer. All indices are recalculated, including tricalcium phosphate saturation
level based upon the water chemistry dosed with the recommended orthophosphate level.
The copolymer requirement is then calculated using a model for tricalcium phosphate scale
control.7 In this case, a model for a commonly used copolymer was used.
The final step is to calculate any other inhibitor requirements such as the phosphonate HEDP for
calcium carbonate scale control. The pH control point of 7.7 limits the requirement in this system.
The recirculating cooling water is barely saturated with calcium carbonate.
Modeling over the operating range encountered for pH, temperature, and water chemistry, allows
for the optimization of a blended formulation which combines the inhibitors in one package, or for
optimization of separate inhibitor feed.
Figure 4 , Figure 5, and
Figure 6 profile the various parameters discussed over the operating range
for the cooling system. Figure 7 profiles the dosage requirement for a blended inhibitor optimized
for the copolymer/phosphate ratio to minimize treatment levels.
The model recommends a higher level of phosphate than is currently employed. Corrosion rates in
the 6 to 10 mpy range are currently observed with a 4 to 6 ppm orthophosphate residual. The
model recommends that 8 to 10 ppm of orthophosphate (as PO4) be maintained to achieve
corrosion rates of 5 mpy or less.
OTHER USES FOR THE MODELS
Figure 8 compares the predicted corrosion rates with, and without, sulfuric acid pH control. The
models predict a much more corrosive water when using acid feed than with a natural cycling of
alkalinity. The addition of sulfate to the water through sulfuric acid feed increases its corrosivity
towards mild steel.
Maintenance of the pH at 7.7 prevents the shift of alkalinity towards the inhibiting carbonate form.
Corrosion rate prediction models can be used to evaluate the impact of acid feed upon water
aggressiveness and corrosion inhibitor requirements as an additional input in evaluating the pros and
cons of neutral versus alkaline treatment programs.
CONCLUSIONS
Models for corrosion rate prediction and treatment level recommendation have been developed
using a combination of laboratory, field and experiential data. The models provide tools for
evaluating a cooling system under varying conditions to determine the impact of operating
parameter changes (e.g. acid feed, concentration ratio, pH) upon water corrosivity and corrosion
inhibitor requirements. Use of the models in computer simulation software allows the chemist to
profile corrosivity and inhibitor requirements of a cooling systems entire operating range rather than
at single points. A combination of models (e.g. corrosion inhibitor and scale inhibitor models) can
be used to optimize the ratio of ingredients in a blended formulation. Corrosion rate and inhibitor
dosage models can provide guidelines to assist an experienced cooling system professional in
optimizing treatment rates and controllable operating parameters. As with any predictive tool, the
models are a supplement to experience - not a substitute for it.
REFERENCES
1 T.E. Larson, R.V. Skold, Laboratory Studies Relating Mineral Quality of Water to Corrosion of
Steel and Cast Iron, Corrosion-NACE 15, 285t (1958).
2 R.A. Pisigan, J.E. Singley, Evaluation of Water Corrosivity Using The Langelier Index and
Relative Corrosion Rate Models, Corrosion/84, Paper No.149, National Association of
Corrosion Engineers, New Orleans, LA, 1984.
3 R.V. Davis,"Investigation of Factors Influencing Mild Steel Corrosion Using Experimental
Design," Corrosion/93, Paper No. 280, National Association of Corrosion Engineers, New
Orleans, LA, 1993.
4 Corrosion-NACE 49 1993.
5 NACE Recommended Formulas, Task Group T3-A-17.
6 Personal communication, Peter Zisson, Buckman Laboratories, Memphis, TN, September,
1992.
7 R.J. Ferguson,"Developing Scale Inhibitor Dosage Models," Proceedings of WaterTech 92,
Houston, TX. (November 11-13, 1992).
TABLE 1
PARAMETERS
MODELED
| |
TABLE 2 PARAMETER RANGE COVERED
|
Parameter | Test Data Range | Units |
Calcium | 6 - 117 | mg/L Ca |
Calcium | | Sulfate | 4 - 631 | mg/L SO4 |
Chloride | | Chloride | 6 - 685 | mg/L Cl |
Sulfate | | Carbonate | 1 - 268 | mg/L CO3 |
Bicarbonate | | Bicarbonate | 76 - 245 | mg/L HCO3 |
Carbonate | | Temperature | 70 - 104 | oFahrenheit |
Corrosion Rate | | pH | 6.4 - 9.2 | pH units |
TABLE 3 COOLING WATER CHEMISTRY
|
Parameter | Makeup Water | Recirculating Water | Units |
Calcium | 62 | 270 | mg/L Ca |
Magnesium | 14 | 76 | mg/L Mg |
Sulfate | 85 | 922 | mg/L SO4 |
Chloride | 138 | 592 | mg/L Cl |
Bicarbonate | 170 | 52 | mg/L HCO3 |
Carbonate | 9 | 1.4 | mg/L CO3 |
Temperature | | 80 - 115 | oFahrenheit |
pH | 8.3 | | pH units |

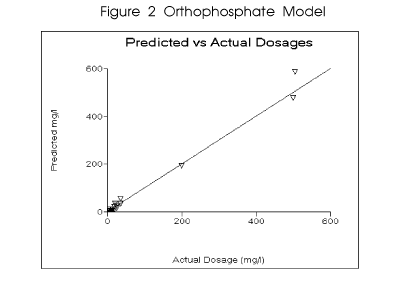
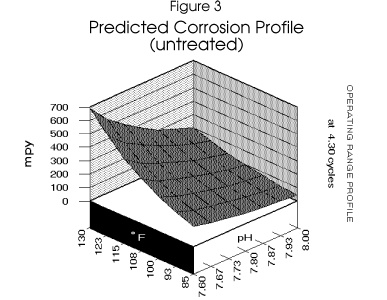
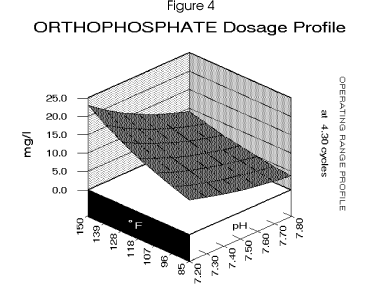
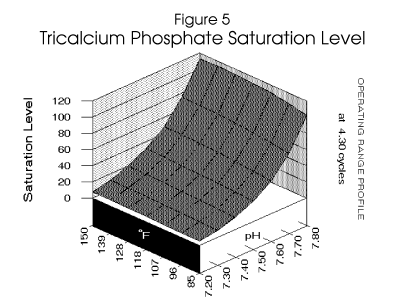
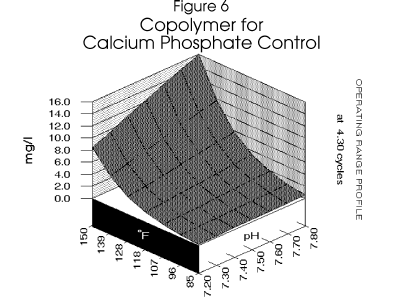
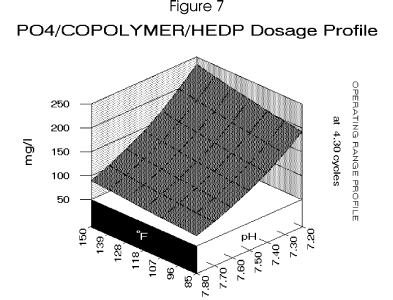
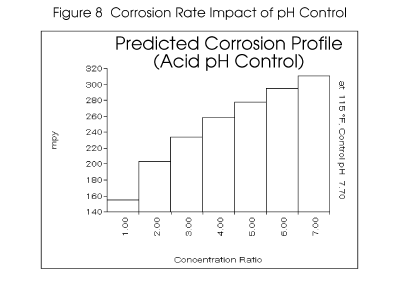
